Alpha Reo: Blazing A Trail in Reinforced Steel Solutions
Alpha Reo: Blazing A Trail in Reinforced Steel Solutions
Blog Article
Top Methods for Optimizing Steel Manufacture Processes for Optimum Performance
From thorough design planning to embracing cutting-edge technologies, the mission for optimal efficiency in steel manufacture involves a complex method. Let's explore exactly how these techniques can change steel construction procedures, paving the means for unmatched performance and competitiveness in the sector.
Efficient Design Planning
In the realm of steel fabrication processes, reliable and strategic design planning plays a pivotal function in simplifying production workflows and making the most of functional productivity. The design of a steel manufacture facility directly affects the performance of procedures, material flow, and employee productivity. By meticulously developing the arrangement of machinery, workstations, storage space areas, and material handling equipment, firms can substantially minimize unneeded movement, reduce material managing times, and maximize the total manufacturing process.
An effective design strategy takes into consideration factors such as workflow sequences, proximity of workstations, product handling routes, and safety policies. It aims to create a streamlined and rational flow of activities from resources intake to the end product dispatch. Through reliable design planning, business can get rid of traffic jams, reduce manufacturing downtime, and boost the total functional effectiveness of the steel construction process.
Furthermore, a well-thought-out layout strategy makes it possible for far better usage of offered area, enhanced communication between employees, and improved security practices within the facility. Overall, spending time and sources in establishing an effective layout strategy can produce significant advantages in regards to enhanced productivity and price savings for steel fabrication businesses.
Advanced Reducing Technologies
Making use of cutting-edge technologies in steel fabrication processes enhances precision, effectiveness, and overall manufacturing high quality. Furthermore, plasma reducing modern technology has actually likewise changed steel manufacture by enabling swift and precise cutting via electrically conductive products. By integrating these sophisticated reducing innovations into steel fabrication processes, manufacturers can considerably raise efficiency, reduce manufacturing times, and inevitably improve the high quality of their products.
Automated Welding Systems

One of the vital advantages of automated welding systems is their capacity to maintain a high degree of accuracy throughout the welding procedure. The precision supplied by these systems guarantees that welds are consistent and meet the called for specifications, bring about stronger and a lot more reliable metal structures. Additionally, automated welding systems reduce the threat of human error, resulting in less flaws and revamp.
Furthermore, these systems can take care of complex welding jobs with convenience, including welding in tight areas or on bent surfaces. This flexibility makes automated welding systems suitable for a broad range of steel manufacture applications, from large-scale commercial tasks to complex custom-made designs. Generally, the implementation of automated welding systems in steel manufacture processes considerably boosts efficiency, top quality, and overall project end results.
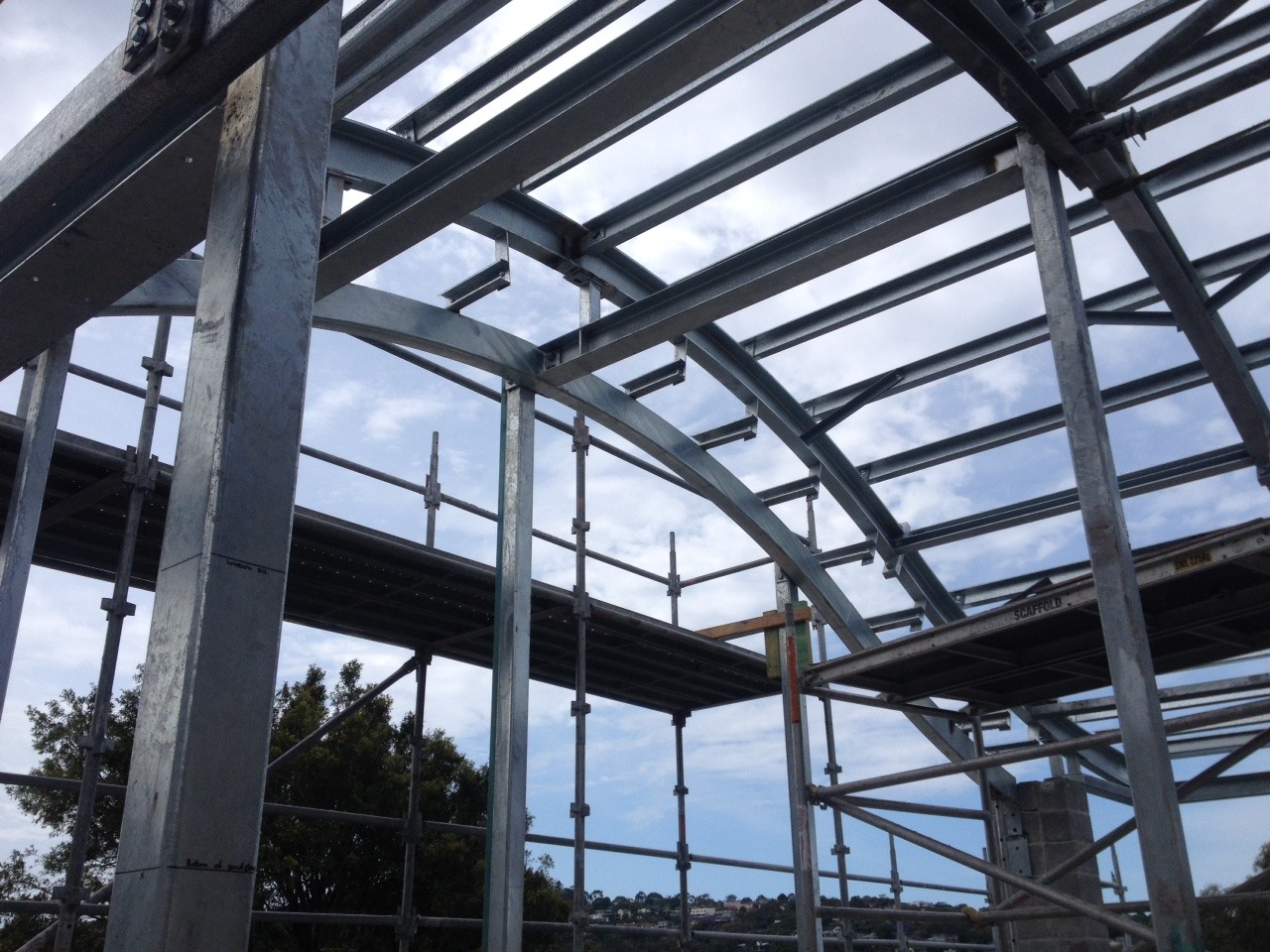
Inventory Monitoring Solutions
Enhancing operational performance and streamlining processes, reliable inventory administration solutions play a crucial duty in maximizing steel construction operations. By implementing durable inventory monitoring systems, steel manufacture firms can ensure that the ideal products are readily available when needed, decreasing disturbances and hold-ups in manufacturing schedules. Using sophisticated software program services enables for real-time monitoring of stock levels, enabling accurate forecasting of material needs and preventing stockouts or overstock scenarios.
Moreover, supply monitoring services assist in lowering lugging costs related to excess stock and enhance cash flow by straightening inventory levels with actual need. By classifying materials based on use regularity and criticality, producers can focus on purchase and storage area allowance, better boosting operational effectiveness. Furthermore, applying barcode or RFID technology assists in accurate inventory tracking and simplifies the tracking of material motions within the center.
Continuous Process Enhancement
To build on the gains made via efficient inventory management remedies, the emphasis currently shifts in the direction of driving continual procedure renovation within steel fabrication operations. Continual process improvement is a methodical technique targeted at enhancing performance, reducing waste, and enhancing general top quality throughout the construction process. By implementing a society of continuous renovation, steel manufacture firms can recognize bottlenecks, simplify workflows, and maximize resources to make the most of productivity.
One trick aspect of continuous procedure enhancement in steel manufacture is the regular testimonial and you could try this out evaluation of production procedures. This includes gathering feedback from employees, checking crucial performance indicators, and determining areas for improvement. By leveraging data-driven insights, companies can make educated choices to drive significant modifications that favorably affect operations.
Moreover, adopting lean manufacturing concepts can considerably add to refine enhancement in steel construction. Alpha reo. Techniques such as worth stream mapping, five company, and Kaizen occasions can help remove non-value-added tasks, systematize procedures, and foster a society of innovation and constant knowing within the organization
Verdict
To conclude, optimizing steel manufacture processes for optimal efficiency needs cautious planning, using sophisticated reducing technologies, applying automated welding systems, taking care of stock effectively, and continually enhancing processes. By integrating these approaches, suppliers can boost performance, decrease costs, and improve general performance in check these guys out the steel fabrication market.
With efficient design planning, companies can remove bottlenecks, minimize production downtime, and enhance the overall operational performance of the steel construction procedure. Alpha reo.
Utilizing sophisticated modern technologies in steel fabrication processes enhances accuracy, effectiveness, and general manufacturing quality. By including these advanced cutting technologies right into steel construction processes, suppliers can significantly enhance effectiveness, reduce manufacturing times, and ultimately enhance the high quality of their items.
Overall, the application of automated welding systems in steel manufacture procedures considerably boosts efficiency, top quality, and overall job outcomes.
One key aspect of continual process enhancement in steel construction is the normal evaluation and evaluation of manufacturing her explanation procedures. (Alpha reo)
Report this page